Vimodrone, April 2022 -Mattei implements Lean Product & Process Development with Milan Polytechnic University.
Even at 100 years old, you can still focus on technological innovation and research & development. This is the case of Mattei SpA, a compressed air manufacturer from Vimodrone, Milan.
Founded in 1919, Mattei is a true micro-multinational, which today has two production sites in Italy, six regional branches on three continents and 250 employees. Its strength is a proprietary technology used in the construction of compressors - rotary vane technology - which permits energy savings of up to 30-40% when compared to the same usage with equivalent "screw" compressors. This distinctiveness has always been combined with a strong focus and investments in research & development along with the choice to entrust University experts for process innovations. From expertise to excellence.
This is how the Lean Product and Process Development project was born, one which has been worked on together since March 2019, by Stefano Murgia, Mattei's technical director, and Monica Rossi, assistant professor at Milan Polytechnic who has a Master's in Management Engineering and a PhD in Management Economics and Industrial Engineering.
“The starting point was the situation Mattei found itself before the project started”, explained Murgia and Rossi. “The emerging picture from the data collection showed that a large proportion of time was spent on reacting to day-to-day responses and that there were difficulties in indicating and establishing priorities. The result was a situation of perpetual emergency, aggravated by an organization structured in “silos”, with no sharing and communications system, little planning and no clearly defined specifications and targets”. Mattei was suffering from what is called “infinite capacity” i.e. the illusion of being able to cope with infinite demands, which in reality just translates into great frustration for both personnel and end clients.
A change of pace and organization was needed, starting with the product engineering process which had to be based on customer requirements. “We introduced documented processes and prioritization of activities, setting up cross-functional teams with different competencies. A central role in this reorganization is assigned to the project manager, who coordinates the necessary resources made available by the various company departments, implements the project, follows its development and guarantees the quality of the project path and the results, while respecting costs and implementation timeframes”.
It was not simply a question of “reviewing the organization” but of suggesting a radical change of approach, moving away from the “silo” culture to one of information sharing, from linear hierarchy to the circularity of teamworking within processes guided by clear priorities. It was not a top-down process, but a tailor-made intervention, where results are measured in the field and the involvement of staff is critical to the success of the transformation.
There are already tangible results too: in 2018/19 it took more than a year to bring a new product to market, whilst in 2021 an entire project plan was created along with two new products being launched; RVXi and RVD for the US market. In 2019 response times to client requests could be as much as several weeks; by 2021 that was down to just a few working days. The conversion of requests into orders has also tripled, a very significant increase in redemption rate. Finally, the time spent on solving daily issues that crop up decreased significantly, freeing up more resources to be spent on design and innovation.
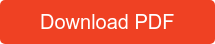