The new machines from Mattei represent a technological revolution that propels the Vimodrone company into the world of Industry 4.0: touch screens, remote control and, real-time notifications in case of anomaly or malfunction, so that you always have everything under control.
Vimodrone, March 2021 – Advanced technologies, with a greater focus on energy-savings, and easy to maintain. The new range of RVXi (Rotary Vane Xtreme) inverter-controlled compressors from Ing. Enea Mattei Spa are so efficient that they herald an efficiency revolution within the variable-speed compressed air industry.
Built specifically to meet the evolving demands of medium-large businesses in the industrial sector, the new range developed from Mattei can count on the new Maestro XC controller, with a 10” touchscreen interface, remote control functions, internet connectivity, linking to company networks or using its built-in modem and real-time notifications via email in case of failure or malfunction: these are just some of the features unique to the new RVXi series which is going to be launched in these days.
“The new Xtreme Communications Technology is in-step with the times and increasingly focused towards Industry 4.0 and Cloud connectivity requirements”. The words of Andrea Capoferri, Industrialisation Manager at Mattei and Project Manager for the RVXi range. “We have carefully analysed the needs of the market to deliver an effective and long-lasting response to the demands of industry, having kept them shoulder-to-shoulder with our R&D team throughout the development”. The first prototype of the new compressors from Mattei had already been presented more than 12 months ago at the Hannover trade fair, but in recent months the company based in Vimodrone (Milan), wanted to be sure their effectiveness was fully tested in the field before proceeding with the actual production. As Capoferri explains: “We wanted to test the machine on a production site in northern Italy to be sure of its effectiveness in real-use conditions and we received excellent feedback right from the outset. After almost 12 months of data collection, we were able to further refine its functionality and now it is finally time to push through with the production of the first batch, closing out a long and demanding year that has been full of successes”.
Alongside the technological developments, Mattei has also focused research into sustainability and energy-savings, which has always been one of the founding principles of the Milanese company’s philosophy. Andrea Capoferri explains: “Our compressors work with oil injection but, unlike our competitors, we use innovative patented technology, called Xtreme Injection Technology, to nebulise the oil allowing it to be injected more intelligently, bringing about significant energy savings”. An innovation for which Mattei was already famous, but which has now taken another step forward with this further development: “We have added an inverter to the Xtreme technology” confirms Capoferri, “It adjusts the compressor rotation speed according to the actual usage, avoiding unnecessary energy waste to make our machines even more efficient across the 40% to 70% capacity range where inverter based control technology is universally deployed by compressor manufacturers”.
But the news doesn’t stop there, as the Industrialisation Manager continues: “Then there is an innovative, smart temperature regulation system called Xtreme Thermal Management Technology; to increase the efficiency of the compression process an oversized cooling system has been designed, managed by our Industry 4.0 ready Maestro XC controller, an electronic thermostatic valve and a variable speed fan, which work symbiotically on the basis of actual oil temperatures, to optimise consumption and operating temperature”.
Other factors which Mattei technicians focused their development attentions on for the RVX are the durability of the materials used and their ease of maintenance, thanks to the presence of flange piping and fittings without the use of sealants, making them easy to maintain as well as being characterised by high reliability in terms of potential leakages.
Another important focus was to be able to monitor compressor parameters in real-time, both via the Maestro XC touchscreen controller, as well as remotely via Mattei Cloud. This is also fundamental for reducing costs because the data can be used to perfectly plan advanced maintenance operations, reducing any risk of failures and being perfectly in line with Industry 4.0 trends.
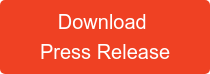