Vimodrone, November 2017 – In the industrial sector, the Life Cycle Cost (LCC) is a recognised method to calculate the full costs of ownership for capital equipment. In the case of industrial machine, this calculation is based on three main factors: capital equipment expenditure (Capex), ordinary maintenance costs and energy-related operating costs.
In a compressor, the running cost is significantly higher than the initial investment and maintenance costs, accounting for up to 90% of the overall LCC. These very high running costs encouraged manufacturers to invest their R&D budgets into conducting specific energy studies to improve their products in terms of increasing energy efficiency and reducing environmental impact.
Mattei has succeeded. Looking at the figures over a five-year life cycle, a rotary vane compressor delivers energy savings of around 20%: this is the lowest LCC on the market. Comparisons with screw compressors vary even more when considering the energy-efficiency performance over a longer period of time.
A screw compressor uses both rollers and thrust bearings with high-tolerance rotors, which operate screws with minimal clearances, thus reducing air leakage and resulting in high volumetric efficiency. However, any of the bearings will wear out over time, inevitably resulting in increased clearances between the rotors and subsequent drops in volumetric performance. This drop in performance equates to a lower air output, varying from manufacturer to manufacturer, which ranges between 30% and 55% over a 10 year period. The performance drop is typically reversed once the screw compressor undergoes maintenance (usually between 40-50,000 hours) substituting all major rolling and thrust components and resetting the compressor to its original tolerances and volumetric performance.
On the other hand, Mattei rotary vane compressors, do not use either rollers or thrust bearings, and rely on hydrodynamic bushings lubricated with oil that do not wear out over time. The injected lubricant, also performs an important sealing action. The advantages of this design are two-fold. Firstly there is no loss in volumetric efficiency over time; secondly a Mattei compressor typically operates for over 100,000 hours without requiring maintenance to replace worn-out bearings. This allowed Mattei to extend their compression unit warranty to 10 years with unlimited usage.
Finally, with Mattei rotary vane compressors, not only does the performance not diminish over time, but it actually improves after the first 1,000 hours of operating. In this running-in period, the blades undergo a further polishing process removing any last asperities, which initiates a microscopic transfer of material that will last for the full lifetime of the compressor.
This has been confirmed by studies carried out by prestigious international research institutes. The most recent of these was conducted by Intertek in the US on a Mattei Maxima 55kW in 2016. During the supervised long-term test, in the first 500 hours Intertek confirmed the finding of a 4% improvement in terms of Specific Energy of the compressor compared to the test results at Zero Hours.
This test also shows that compared to screw compressors, whose best performance is recorded at zero hours, a rotary vane compressor delivers a significant improvement in energy efficiency at zero hours after just a short period of operation.
The analysis conducted with the Lifecycle Costing method demonstrates that a Mattei compressor is a safe and reliable investment in the long term not only in economic terms, thanks to a reduction in maintenance costs, but also in terms of environmental impact. It should not be forgotten that one of the main factors contributing to greenhouse gas emissions, responsible for global warming, is the consumption of electricity. 50% of this consumption is attributable to the industrial sector, and of this, the production of and delivery to end users of compressed air makes up around 20%.
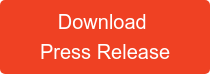