Compressed air is vital for industry as it drives many production facilities and pieces of equipment. Its use is responsible for more than 10% of industrial energy consumption, meaning the choice of compressor becomes essential when looking to maintain control of energy costs. The English company Luxfer Gas Cylinders is an excellent example of obtaining efficiency in this regard.
Luxfer Gas Cylinders is the world’s largest manufacturer of high-pressure aluminium and composite gas cylinders which are light, durable and corrosion-resistant for a wide variety of applications - such as life support for fire fighters, alternative fuel for transport, oxygen or special gas blends for medical services, emergency slides for commercial aircrafts or helicopter utility float systems, and nitrous oxide cylinders for boosting engine performance in professional racing. The company operates in the US, Canada, China, India and the UK.
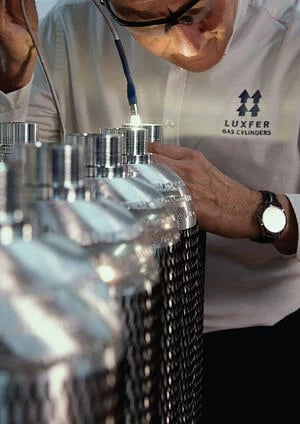
Their UK site is located in Nottingham where over 80 pieces of equipment are employed to produce the cylinders. Most of the machines are bespoke to their processes and have some form of pneumatic actuation. For example, hydraulic presses with auxiliary pneumatic actuation and handling capabilities are used for aluminium extrusion and forming. Specialist threads and forms to aluminium are made by machinery with pneumatic actuation. Handling is carried out by robotics with pneumatically operated grippers, and by conveying and handling apparatus with pneumatic actuation.
Considering many of the environments where their cylinders can be seen in action, their products have to withstand some of the toughest conditions, whether that be in the skies, the midst of fires or the deep sea. They often contain flammable, explosive or volatile gasses, and combined with the aggressive climates in which they function, they must meet standards such as BS EN ISO 7866:2012 and comply with European Directives such as 2010/35/EU (Transportable Pressure Equipment Directive) or 2014/68/EU (Pressure Equipment Directive). Steve Pikett, the site services and tool-room manager explains: “Every cylinder undergoes mandatory pressure testing, and samples are routinely ‘tested to destruction’, using hydraulically-driven and pneumatically controlled equipment.”
All compressed air needs for their equipment were served by two existing Mattei compressors, which have been running reliably for 25 years. However, production requirements have changed over this time. In addition, the company was planning to move production from another site to the Nottingham factory. The need for a new compressor to increase their capacity provided an ideal opportunity to assess whether the existing units were suitable for their current processes, and identify ways to reduce the amount of energy consumed by air compression.
Martin Chitty, Business Development Manager at Mattei Ltd, says: “To evaluate their compressed air needs and the efficiency of their system, we conducted a data logging survey using Mattei’s Intelligent Energy Management (MEIM) equipment. We recorded the total electrical consumption of each compressor every 15 seconds over a seven-day period, and in accordance with ISO 11011:2013, the international standard for compressed air energy efficiency assessment. Based on the measurements, we recommended a new Mattei Maxima Xtreme 75 compressor.”
Free of the blow-holes and leakage issues which are inherent in screw compressors, Mattei’s vane compressors can operate at low speeds from a direct-drive coupling. This means they are more volumetrically efficient. The Maxima Xtreme utilises Mattei’s latest oil injection technology as well as its new high-performance oil in order to further minimise power consumption. The Maxima has a rotational speed of only 1000 r.p.m and its constant speed is ideal for a manufacturer such as Luxfer Gas who use large, constant volumes of compressed air for long periods.
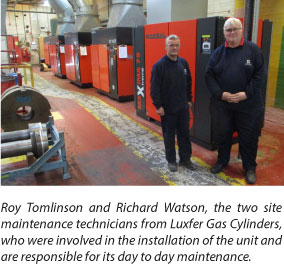
“We had considered other manufacturers, but Mattei where chosen due to their proven track record working with us,” says Steve Pikett. “Based on the data extrapolated from the survey, Mattei recommended using the Maxima Xtreme 75 to meet base load requirements. When further demand is needed, our existing compressors can come online. This way, we can lower our energy consumption, save costs and reduce our carbon footprint.”
The compressor was installed in advance of the planned increase in production. To provide the business with the ability to save even more energy in the future, an extension to the ducting base has been installed which would enable the factory to integrate a heat recovery system. This would enable Steve and his team to recover most of the waste heat generated by the compressors and use it for space or water heating.
In the meantime, Steve concluded that the Mattei Maxima Xtreme 75 has been a welcome addition to the site. “It’s simple and straightforward to operate, and monitoring of its energy usage as well as the air itself has provided positive results.”
From Vane Magazine 15, September 2019
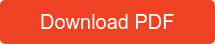