Innovation and industrialisation. This is the combined focus on which the Mattei Group aims to grow, creating innovative products that can anticipate and respond to the demands of a rapidly evolving marketplace.
Ida Costanzo, an engineer with a Masters in Energy Engineering, several publications in scientific journals and at international conferences, has been at Mattei since 2015 as the group’s Innovation Manager. One of the many professionals in our Innovation division that manages the journey from an idea or concept through to the realisation of the prototype.
Andrea Capoferri, a mechanical engineer and in Mattei since 2007, is the Industrialisation Manager and the project manager for the RVXi series; the new line of inverter controlled Mattei compressors launched at the Hannover Fair in 2019 and put into production in March 2021. His task is to take developments from prototype to final product, addressing and resolving any critical issues by standardising solutions that will deliver the high performance engineered into the prototype.
Their main focus of investigation and experimentation relates to the unique rotary vane compressor technology, where Mattei stands out, allowing it to compete with the giants in the market. “Ours is a totally different technology from the “screw” compressors which are much more widespread”, explains Capoferri. “Making a rotary vane compressor requires a higher level of technological capability, which in turn offers many distinct advantages”.
The first of these is energy savings. Costanzo explains: “From studies carried out in-house and later confirmed by qualified international bodies, it emerges that for the same amount of compressed air produced, the introduction of rotary vane technology in a compressed air production plant can generate energy savings of between 30 to 40%. This increases customer profitability as it results in thousands of euros of savings each year for our clients”.
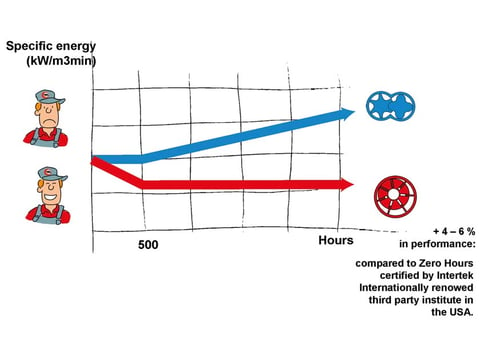
And there’s more: in Mattei rotary vane compressors there are no thrust forces thus, the journals of the compression unit are supported by white metal bushings which are not subject to wear. Conversely, ball or angular roller type bearings are used in screw compressors to counter their internal thrust forces, this results in bearing wear and the need for replacement.
There is also another advantage linked to the life-cycle of the compressor: “The efficiency of Mattei rotary vane compressors do not decline over time, as it does with screw compressors. Experimental data verifies that it improves over the first 500 hours of operation. The components in relative motion actually undergo an adaption that improves their tribological behaviour, leading to an additional reduction in internal friction”, explain Costanzo and Capoferri. If we were looking at graphically describing the performance of a rotary vane compressor in terms of specific energy (kW absorbed compared to the flow delivered): in the first 500 hours we will have a line that drops rapidly and then settles in at an optimum value for the rest of the product’s life. A screw compressor on the other hand, sees its specific energy curve increase from zero hours onwards due to the wear of internal components.
Energy saving, performance, environmental sustainability and durability of materials are the hallmarks of rotary vane technology and the areas on which the R&D department focuses its attention.
The synthesis and application of this research has led to the birth of Xtreme Injection Technology, a proprietary technology that allows the exact amount of oil to be dosed through atomisation to ensure high operating standards, whilst reducing energy consumption and environmental impact.
A further result of Mattei research is Xtreme Thermal Management Technology, an oversized cooling system managed by an electronic thermostatic valve and a variable speed fan, controlled by the Maestro XC controller, which allows the oil temperature to be adjusted to optimise energy consumption rates.
Another innovation that allows the best use of energy resources is the application of an inverter to adapt the rotation speed of the compressor according to plant air demands, avoiding energy waste and optimising efficiency.
But where does the focus on constant innovation that characterises the vision of the Mattei Group come from?
“This is a key element of the overall company strategy,” Capoferri and Costanzo explain, “which on one hand aims to renew the range of design, yet at the same time looks to constantly implement improvements into existing products. Some points of investigation also come from listening to the customer in getting feedback from them and our distributors around the world. In responding to them we give rise to a real continuous improvement cycle that is nourished by close and constant dialogue with our customers”.
The Innovation division of Mattei is in constant contact with main bodies and research centres, including the Milan Polytechnic. Alongside product innovations, it is also involved in research into new materials and applies its skills, knowledge, and experience in complementary fields, such as the creation of expansion systems for energy production.
From Vane Magazine 19, February 2022