MATTEI FAVOURS GREEN INDUSTRY
In Denmark, the very strict regulations in environmental matters have led to the development of an intense green culture. The most modern and completely automated farms use cutting-edge technologies for the purpose of optimizing the production chain, and hence avoiding any wastage: even organic waste can be reused to obtain methane to feed the national gas distribution network.
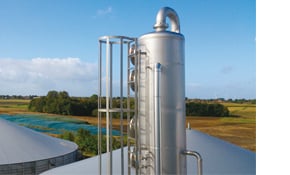
MATTEI AND JA TRYKLUFT, SPECIALIZED IN COMPRESSED AIR FOR THE DANISH FARMS
JA Trykluft ApS, a Danish company owned by Johan Kold and Andreas Skjold, is the local distributor for Mattei gas and air compressors.
Established in 2005, the company has grown and gained a noteworthy industrial experience, particularly in relation to the big farming businesses using production processes that are both highly technological and automated. In Northern Europe, JA Trykluft is today a leading distributors of special units for compressed air supply employed in the automated milking system.
The now consolidated cooperation with Mattei, has recently led to the development of some important environmental projects - a matter of great concern in Denmark, which is linked to very strict regulations but also significant subsidies for companies.
THE BIOGAS UPGRADING ACCORDING TO AMMONGAS
One of the most interesting partnerships is that with Ammongas, a Danish consulting and engineering company, designing and implementing environmentally friendly solutions for the purpose of purifying air and gas, removing bad odours and emission control from industrial sites and biogas upgrading.
“By means of our cutting-edge and in many cases even unique systems for the technology employed, large quantities of biogas produced by Danish intensive breeding farms can be captured for being treated and fed into the national gas distribution network,” Mr. Dan Haarh Madsen, Production Manager of Ammongas A/S, says. “The system equipped with the exclusive rotary vane technology by Ing. Enea Mattei SpA allows for feeding methane produced from biomass into the upgrading system, which creates an optimum return, even in terms of maximum economic efficiency.”
In 2015, Ammongas delivered the first of a series of projects to a large farm near Skive, Denmark. This plant operating at very low pressure (close to zero) is able to transform biogas with a 37% of CO2 concentration deriving from organic waste into 99% of pure methane. Another advantage is the fact that there is no dispersion into the atmosphere. The methane is then compressed, taken to major pressure levels and dried, in order to have the physical properties necessary for being fed into the Danish gas distribution network.
VANE TECHNOLOGY: EFFICIENCY, RELIABILITY AND PRECISION
All new Ammongas systems are equipped with Mattei rotary vane technology. The compressors used during the methane compression stage are part of the AGC series with power ranging from 30 to 55 kW, equipped with an inverter-based variable speed-adjustment system. In addition to Skive, the AGC compressors are the core of other systems such as those installed in Ivar, Norway.
“Along with a dedicated software, which has been especially developed for this kind of applications, the inverter enables to adjust the supplied flows to the real amount requested. The compressors are integrated in a larger, very delicate and complex system; the gas flow is scrupulously controlled so that it can be fed in a calibrated way into the gas distribution network. In order to ensure maximum efficiency, the compressors are networked and reply to the plant’s actual need avoiding any waste of energy,” explains the engineer Mr. Andrea Capoferri, Senior Technical Manager at Mattei, who was in charge of the project in cooperation with Johan Kold and Andreas Skjold from JA Trykluft.
“One of the system’s most critical issue is the gas flow control: Mattei has developed a Master Controller that is able to recognize and notify by means of a warning signal when the set point is reached before the biomasses from the big digesters, where fermentation takes place, are injected into the compressor,” Mr. Andreas Skjold adds.
A TEAM WORK FOR AN INNOVATIVE AND HIGHLY CUSTOMIZED PRODUCT
“The application for Ammongas required a great effort in order to create unrivalled machines, which best suits the customer’s requests. We have designed a software performing a reverse control function,” the engineer, Mr. Capoferri, explains. “Before introducing the methane into the compressor, the measuring device assesses that flows are set up conforming to the parameters set by the user. The control system developed by Mattei is very precise in adapting the flows to the real need with a margin of error below 1%”.
“Over these years, the cooperation with JA and Ammongas has led to a product with both water and air cooling solutions aiming at the continuous improvement of the energetic recovery value,” Mr. Capoferri concludes.
Big farming businesses are obliged to comply with the extremely strict environmental standards, receiving on the other hand subsidies for implementing green projects.
“We have offered Ammongas a very competitive product that ensures top performance,” Mr. Andreas Skjold states. “The results achieved by means of the Mattei compressor go far beyond expectations. The abatement of energy consumption has been a real surprise, just like the reduction of noise pollution, which is rigorously controlled in Denmark.”
“The multiple pluses of the Mattei technology turn into extraordinary performance along with a high level of energy efficiency as well as significant reliability, an aspect that is not to be underrated in hazardous environments such as those we can find with gas applications,” state Mr. Presotto, Export Area Manager and Lorenzo Sangalli, Custom Product Manager of Ing. Enea Mattei SpA. “In addition, thanks to the excellent quality of component, there are minor maintenance and repair costs in the long run.”
G & GC SERIES
Mattei’s rotary vane Gas Compressors are designed to compress sweet, sour and bio gasses. The range covers 4kW up to 200kW available as a stand-alone gas end for local packaging or as customer specification gas compressor packages. All versions come complete with automatic flow control at a constant delivery pressure, integrated or remote cooler and threaded or flanged gas intake facility. The compressors are compact and easy to install, offering reliable operation and constant performance throughout time.
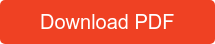