MAXIMA ALWAYS IN POLE POSITION, EVEN IN TOUGH ENVIRONMENTS
There is a long-standing relationship between Mattei and the South Ferriby site of the giant CEMEX. The efficient and reliable Mattei compressors had been working tirelessly for more than 25 years until the plant was badly damaged, due to heavy flooding. Mattei then won the Motion Control Industry Award for the project of the year for their part in the replacement of the damaged compressors.
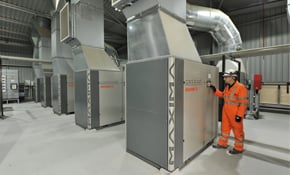
EXTREME CONDITIONS FOR THE COMPRESSED AIR
The use of compressed air in quarries and cement plants is fundamental. These are interesting industries, with many environmental challenges and there is no limit for the potential uses of compressors: from mining to production, to packing the final product.
Durability and reliability are the essential qualities of a compressor, when it is used for many hours in environments exposed to abrasive powders and severe atmospheric conditions. If, in addition, there is a large use of compressed air, the cost of this supply can be very significant and therefore the specific energy efficiency of the compressed air equipment is vitally important. CEMEX at South Ferriby, part of the International group and a leader in the production of building materials, is well aware of this fact and has chosen the rotary vane technology of Mattei compressors for more than 25 years.
EXCELLENT FUNCTIONING FOR OVER 200.000 HOURS
CEMEX, headquartered in Monterrey, Mexico, is a solid multinational with plants all around the globe. It employs 40,000 people and has a business volume of 15 billion dollars. In the United Kingdom, where its subsidiary employs 3,500 people, CEMEX has a cement mining and production site in South Ferriby. Here, about 30 Mattei compressors have been smoothly operating for more than 25 years, including a variety of models such as the Classic ERC series, the highly efficient Maxima 75 machines, and variable speed Optima compressors as well as some smaller units.
“Over the years, Mattei’s compressors have proven to be incredibly reliable, also in difficult environments, like quarries and cement plants,” Mr. Andy Jones, Managing Director of Mattei Compressors Ltd states. “These machines at CEMEX have had a hard life, many of them working for more than 200,000 hours still with their original rotor stator units (airends), wear-free and with only modest maintenance interventions required.”
“The superiority of our rotary vane technology compared to screw compressors is evident: In the course of time, this site has installed some screw compressors, which however did not produce the required results in terms of efficiency, reliability and durability. Mattei’s vane compressors did however stand the test of time and they are volumetrically efficient and have a low rotational speed (from 1,000 rpm); whereas a screw compressor must operate at 3,000 rpm and above to achieve a similar result,” Mr. Jones continues.
CEMEX CONFIRMS MATTEI TWICE
The value of the Mattei technology was also demonstrated after a serious flood at the end of 2013, which seriously damaged the South Ferriby plant. “In the compressor replacement project, Mattei beat its competitors,” Mr. Jones remembers. “Alongside the reliability of our machines, the Mattei team played a fundamental role, by presenting innovative solutions. CEMEX chose the high-performance models Maxima 75 and Optima 90 and the latest generation Master Controller Concerto. This device is able to command and control up to 16 compressors, even of different brands, regulating the air flow rate, depending on the plant’s real need. This turns into energy savings of more than 35%.”
The quality of the Mattei products is also confirmed by Mr. Nigel Appleyard, Maintenance Manager of CEMEX: “CEMEX conducted a rigorous tender process before selecting Mattei to supply a new compressed air facility with a fixed 10 year maintenance contract. With the centralisation of the equipment, and the installation of a new ring main, the business has achieved a substantial energy improvement, improved air quality and fixed maintenance costs”.
BEST 2016 PROJECT: MATTEI WINS THE MOTION CONTROL INDUSTRY AWARD
In 2016, Mattei’s installation at the CEMEX South Ferriby site was awarded the Motion Control Industry Award in the Project of the Year category. The Jury prized the versatility, reliability and efficiency as winning features. “We are really proud of this recognition, especially if you consider that it has been awarded for the very first time,” Mr. Andy Jones comments. “The research for tailor-made solutions for any single client is a sort of trademark for Mattei and receiving the Motion Control Industry Award, is very pleasing and a recognition of the excellent work the team at Mattei has done.”
CLASSIC SERIES
Open frame ERC compressors are used in various applications, including those in the energy, manufacturing and automotive sectors. The machines are available in the version mounted on base or on the air tank and have powers from 1.5 kW to 55 kW. They are complete with final air cooler, separator and condensate drain. The low noise level allows it to be used even in the absence of soundproof cabins.
MAXIMA SERIES
MAXIMA High Efficiency compressors are designed to operate at only 1,000 rpm and can work for more than 100,000 hours. The best air quality is guaranteed by a filter system with a specific efficiency of 99%, while the three-phase oil separation system is able to reduce oil particles in the air to <1 ppm. High-Efficiency compressors reduce the oil usage by about one third and use half the lubricant required by a traditional rotary screw compressor. They are available with power from 30 kW to 160 kW.
OPTIMA SERIES
Variable speed OPTIMA Series compressors automatically adjust the operations according to the load profile. The compressor inverter automatically adjusts the motor's rotational speed to ensure that the air emitted by the system always matches the real-time demand.
With direct coupling and power from 11 kW to 200 kW, OPTIMA series compressors have undoubted advantages in terms of reliability and strength, reduced operation and maintenance costs. They are also environmentally friendly thanks to a very low lubricant usage compared to traditional screw compressors.
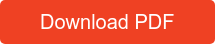