Lerma Gomme was established in 1986 and specialises in tyre recycling: a sector which is generating growing interest given the increase in attention paid to the environment and, in particular, to sustainable waste management.
MATTEI EFFICIENCY APPLIED TO THE TYRE RECYCLING PROCESS
In fact, tyres are very difficult to dispose of given that they take about 100 years to deteriorate when buried in landfills; retreading, on the other hand, actually doubles their working life (and even triples for industrial vehicle tyres) and reduces the disposal flow rate of such products.
.jpg?width=355&name=Lerma_Gomme%20(1).jpg)
Lerma Gomme has steadily increased its sales figures over the years, and is now recognised as one of the major tyre retreading enterprises in North-Western Italy.
It currently has sixteen employees working at four different branches: Lerma Gomme has its main production plant in Silvano d’Orba, in the province of Alessandria, and three customer support centres in the provinces of Alessandria and Genova.
Over the last ten years, the company has focused on the manufacturing of off-road tyres.
It supplies a widespread market throughout Italy and serves both end consumers and tyre workshops.
Further to the three support centres, end customers can also order tyres online from the corporate website.
“A sales channel whose volumes continue to increase”, explains Claudio Arecco, cofounder and current CEO of Lerma Gomme. “The number of customers purchasing tyres online continues to grow, and recently we also started receiving orders from abroad”
RETREADING TYRES: A MARKET ON THE UP
It is possible to retread tyres because the actual working life of the structure greatly exceeds that of the tread: a vulcanisation process is used to blend the new and old parts together, creating a retreaded tyre where the old worn tread is replaced by new material that has identical structural features as the original.
The retreading process is regulated by specific Technical Standards (UN ECE Regulation no. 108 for cars and UN ECE Regulation no. 109 for commercial vehicles) which involves careful selection and monitoring of certain parameters which are vital for the quality of the final product, including centering and balancing tests.
The advantages of recycling are first and foremost of an environmental nature, but this also generates an exceptional quality/ price ratio of the final product.
The benefits for the environment can be summarised in a few key figures: the changing of tyres in Europe each year leads to the manufacturing of 140 million wheels a year.
Between 20 and 28 litres of crude oil are required to produce each tyre, a figure which drops significantly to 5.5 litres for retreaded tyres.
About 80% of the old tyre is preserved during the retreading process: when compared with the production of a new tyre, this recycling process also generates a 70% saving in energy.
Then there is also the saving on materials that form the steel tension rod, bead and carcass to consider.
In 2002 Italy introduced a directive where the Public Administration is obliged to purchase retreaded tyres for a total of 20% of the total amount of replacement tyres bought each year.
The Italians who choose retreaded tyres save over 26 million Euro every year, which corresponds to a total savings of 180 million litres of oil and 51,400 tons of other raw materials such as natural and synthetic rubber, textile fibres, carbon black, steel and copper.
HOW RETREADING IS ACHIEVED
“Every single tyre is retread with a high-performing mixture and the experience gained in over 25 years on the market, along with our production methods and processes, allow us to offer our customers a warranty which is equal to that granted on new tyres”, explains Claudio Arecco.
The retreading process is divided into six main phases. To start with, the carcass is carefully inspected to ensure it is suitable for retreading; each carcass then undergoes the buffing phase, to remove all old residual tread, followed by the rubberising phase where the new tread is applied to the carcass.
The next phase consists of balancing the tyre so as to achieve perfect equilibrium.
The tyre is now ready for the curing phase in a high temperature mould, so that the tread is completely enveloped by the rest of the tyre and the established tread pattern is applied.
The finished product is inspected again to ensure the retreading has been completed to the required standard.
LERMA GOMME AND MATTEI, A LONGSTANDING PARTNERSHIP
“The tyre moulding phase is a particularly important phase of the tyre retreading process”, explains Claudio Arecco. “A top quality compressed air supply is absolutely essential to ensure all operations run smoothly. We also need sturdy machinery which is able to withstand the huge amount of working hours that our process requires”.
Based on this core requirement, Lerma Gomme recently confirmed Mattei as its partner for the supply of compressed air: “We have been using a Mattei compressor for some time now”, continues Claudio Arecco “and we are highly satisfied with its performance. We needed to purchase a new machine to increase our production rate and we chose the latest ERC 22 HH Mattei, a highly robust and reliable compressor, designed to operate non-stop and specifically dimensioned to meet our requirements”.
“I have extensive experience in this sector”, concludes Claudio Arecco “and I was the one who chose this extremely hard-wearing and very low-maintenance machine. I would say that these machines are designed to work: the more they work, the less they break. I must also say I am extremely impressed with the support services provided by Mattei although, as I was saying, we have used them very occasionally: thank goodness!”
MATTEI ERC COMPRESSOR
ERC belongs to the Mattei Classic rotary vane compressor range: they come complete with air cooler, separator and electronic condensation exhauster, which are noticeably silent making them ideal for use even in stations without soundproof cabins.
The ERC compressors are fitted with a three-phase asynchronous electric motor running in continuous, modulated or automatic mode. The control panel has a protection rating of IP54 to operate efficiently even in dusty and humid environments. The electromechanical control panel is fitted with a range of control buttons: start, stop, reset block, emergency plus warning indicator lamps and an hour meter.
The ERC motor has a direct flexible coupling drive system. The built-in cooling unit has an aluminium radiator to cool the oil and compressed air. The air cooler is also fitted with a condensation separator and timed exhaust system. Oil separation occurs in three phases using coalescent filters.
The compressor-motor unit is anchored to a robust base unit with an open frame for easy lifting and handling operations.
ERC 22 HH supplies compressed air at a pressure of 13 bar and has a rated power of 22 kW; maximum flow rate reaches 2.57 m3/min.
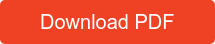