I pneumatici usati sono infatti rifiuti di difficile smaltimento, che richiedono circa 100 anni prima di deteriorarsi quando interrati in discarica, e la loro ricostruzione permette di fatto di raddoppiarne la vita (e addirittura di triplicarla per le gomme dei veicoli industriali), rallentando così il flusso di smaltimento di questi prodotti.
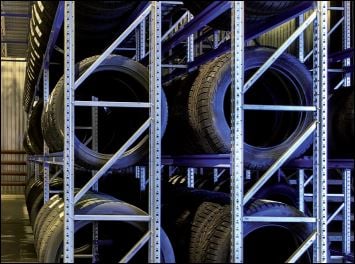
Negli anni Lerma Gomme ha incrementato stabilmente le proprie vendite, fino ad affermarsi come uno dei maggiori ricostruttori di gomme dell’Italia nord-occidentale. Oggi è una realtà con sedici dipendenti e quattro sedi: accanto allo stabilimento produttivo di Silvano d’Orba, in provincia di Alessandria, Lerma gomme opera con tre punti di assistenza diretta ai clienti, sul territorio delle province di Alessandria e Genova. Nell’ultimo decennio, l’azienda si è specializzata nella produzione di gomme per il fuoristrada.
Il mercato servito non è solo quello locale, ma si estende a tutta l’Italia e comprende sia utenti privati che gommisti. Gli utenti finali, oltre che presso i tre punti di assistenza, possono anche ordinare le gomme direttamente dal sito web dell’azienda. “Un canale di vendita sempre più frequentato”, spiega Claudio Arecco, socio fondatore ancora oggi alla guida di Lerma Gomme. “Il numero di clienti che comprano online è in crescita, e da qualche tempo abbiamo iniziato a ricevere ordini anche dall’estero”.
LA RICOSTRUZIONE DELLE GOMME: UN MERCATO DESTINATO A CRESCERE
Ricostruire uno pneumatico è possibile perché la sua struttura ha una vita utile molto più lunga di quella del battistrada: attraverso un processo di vulcanizzazione, le parti vecchie e nuove si fondono, dando vita ad una gomma ricostruita, dove il battistrada usurato viene sostituito con materiale nuovo, che ha caratteristiche strutturali pari all’originale.
Il processo di ricostruzione è regolato da norme tecniche specifiche (Regolamento ECE ONU 108 per le vetture e Regolamento ECE ONU 109 per i veicoli commerciali) e prevede un’attenta selezione e la verifica di alcuni parametri fondamentali per la qualità del prodotto finale, quali i controlli relativi alla centratura e all’equilibratura.
I vantaggi del riciclaggio sono prima di tutto di ordine ambientale, ma si traducono anche in un ottimo rapporto qualità/prezzo per il prodotto finito. Per comprendere i benefici per l’ambiente, basta citare alcuni numeri: in Europa ogni anno il cambio di pneumatici comporta la produzione di 140 milioni di ruote all’anno; per realizzare ciascuno pneumatico vengono consumati tra i 20 e i 28 litri di greggio, che si riducono a 5,5 litri nel caso di pneumatici ricostruiti. La ricostruzione permette di preservare complessivamente l’80% dello pneumatico: in confronto alla produzione di uno pneumatico nuovo, attraverso questo procedimento di riciclaggio si risparmia il 70% di energia. A questo va aggiunto inoltre il risparmio relativo ai materiali di cui sono composti il tallone, la carcassa e l’asta di tensione in acciaio. Dal 2002 è stato introdotto nel nostro Paese l’obbligo per la Pubblica Amministrazione di destinare almeno il 20% degli acquisti di pneumatici di ricambio ai ricostruiti. Ogni anno gli italiani che scelgono il ricostruito risparmiano oltre 26 milioni di Euro, che corrispondono ad un risparmio di180 milioni di litri di petrolio e 51.400 tonnellate di altre materie prime come la gomma naturale e sintetica, fibre tessili, nero fumo, acciaio e rame.
COME AVVIENE LA RICOSTRUZIONE
“Ogni nostro pneumatico viene ricostruito con una mescola altamente performante e grazie alle nostre metodologie di lavoro e all’esperienza maturata in oltre 25 anni, possiamo offrire sui nostri prodotti ricostruiti una garanzia pari a quella degli pneumatici nuovi”, spiega Claudio Arecco.
Il processo di ricostruzione si articola in sei fasi principali. Inizialmente viene effettuato un controllo accurato della carcassa, per stabilire se è idonea alla ricopertura; quindi, ciascuna carcassa idonea viene sottoposta a raspatura, per privarla della gomma residua sul battistrada, e poi a gommatura, operazione che consiste nell’aggiungere alla carcassa il nuovo battistrada.
Il passo successivo consiste nel bilanciare la gomma per ottenere una perfetta equilibratura. A questo punto lo pneumatico è pronto per esser vulcanizzato in una pressa ad alta temperatura, in modo tale che il battistrada diventi un tutto unico con la copertura, dove viene stampato con la geometria del disegno stabilito. Il prodotto finito viene nuovamente controllato per appurare la perfetta riuscita della ricostruzione.
LERMA GOMME E MATTEI, UN LUNGO SODALIZIO
“La fase di stampaggio delle gomme è un momento particolarmente importante nel processo di ricostruzione degli pneumatici”, spiega Claudio Arecco. “Perché tutto funzioni al meglio, è fondamentale avere una fornitura di aria compressa di qualità. Abbiamo inoltre necessità di macchine solide, in grado di affrontare le molte ore di lavoro che il nostro processo richiede”.
A partire da queste esigenze, Lerma Gomme ha scelto di recente di confermare Mattei quale suo partner per la fornitura di aria compressa: “Abbiamo già in azienda da parecchi anni un compressore Mattei”, continua Claudio Arecco “E proprio perché molto soddisfatti delle sue prestazioni, quando per l’aumentare della mole di lavoro abbiamo dovuto pianificare l’acquisto di una nuova macchina, la scelta è ricaduta sul nuovo ERC 22 HH Mattei, un compressore robusto e affidabile, studiato per lavorare in continuo e dimensionato sulle nostre necessità”.
“Ho una lunga esperienza nel settore”, conclude Claudio Arecco “e ho scelto personalmente questa macchina, perché è molto resistente e richiede una bassissima manutenzione. Direi che queste sono macchine nate per lavorare: più lavorano, meno si rompono. Posso dirmi soddisfatto anche del servizio di assistenza fornito da Mattei, che comunque, come dicevo, abbiamo utilizzato poco: fortunatamente!”
IL COMPRESSORE ERC MATTEI
ERC fa parte della gamma di compressori rotativi a palette Mattei Classic: compressori completi di refrigeratore dell’aria, separatore e scaricatore elettronico di condensa, che si distinguono per la bassa rumorosità e sono idonei all’uso anche in stazioni prive di cabina insonorizzante.
Dotati di motore elettrico asincrono trifase, i compressori ERC operano con modalità di funzionamento continuo modulato e automatico. Il quadro di comando ha grado di protezione IP54 per operare con efficienza anche in ambienti polverosi e umidi; il pannello di comando elettromeccanico è dotato di pulsanti di avviamento, arresto, ripristino blocchi, emergenza, spie di segnalazione e conta-ore.
Il motore di ERC funziona per accoppiamento diretto tramite giunto elastico. Il gruppo di raffreddamento integrato ha radiatore in alluminio, per il raffreddamento dell’olio e dell’aria compressa. Il refrigerante dell’aria è inoltre dotato di un separatore di condensa e scaricatore temporizzato. La separazione dell’olio avviene a tre stadi mediante filtri coalescenti. Il gruppo compressore-motore è fissato su un robusto basamento, dotato di aperture che consentono un agevole sollevamento e movimentazione.
ERC 22 HH fornisce aria compressa a una pressione di 13 bar ed ha potenza nominale di 22 kW; la portata massima è di 2,57 m³/min.